A new kind of way to maintain balcony glazing systems
The chairman of the board of a housing corporation was scratching his head. Shareholders Virtanen and Korhonen had for some time complained that the balcony glazing systems were in bad condition and same complaint was raised from Nieminen. There were wear and tear in hinges and guides even the seals were broken and locks did not work. Didn’t we just install those like ten years ago, wondered the chairman? Surely they dont need any renevation at this point, thats expensive..
In Finland there are over a million balcony glazing systems built but there is barely any regulatory requirements for maintenance. Neglected maintenance can at worst lead to dangerous situations where the glass can fall and cause extensive damage. Housing companies usually take notice when complaints from occupants start piling up. Very often at this point it can mean that the whole balcony glazing needs to be redone even though the glass itself is intact and in good condition. They can survive the test of time but what cant is the plastic parts that degrade over time and start to go brittle or even break. Typical life age of those parts is about ten years before need to change arises.
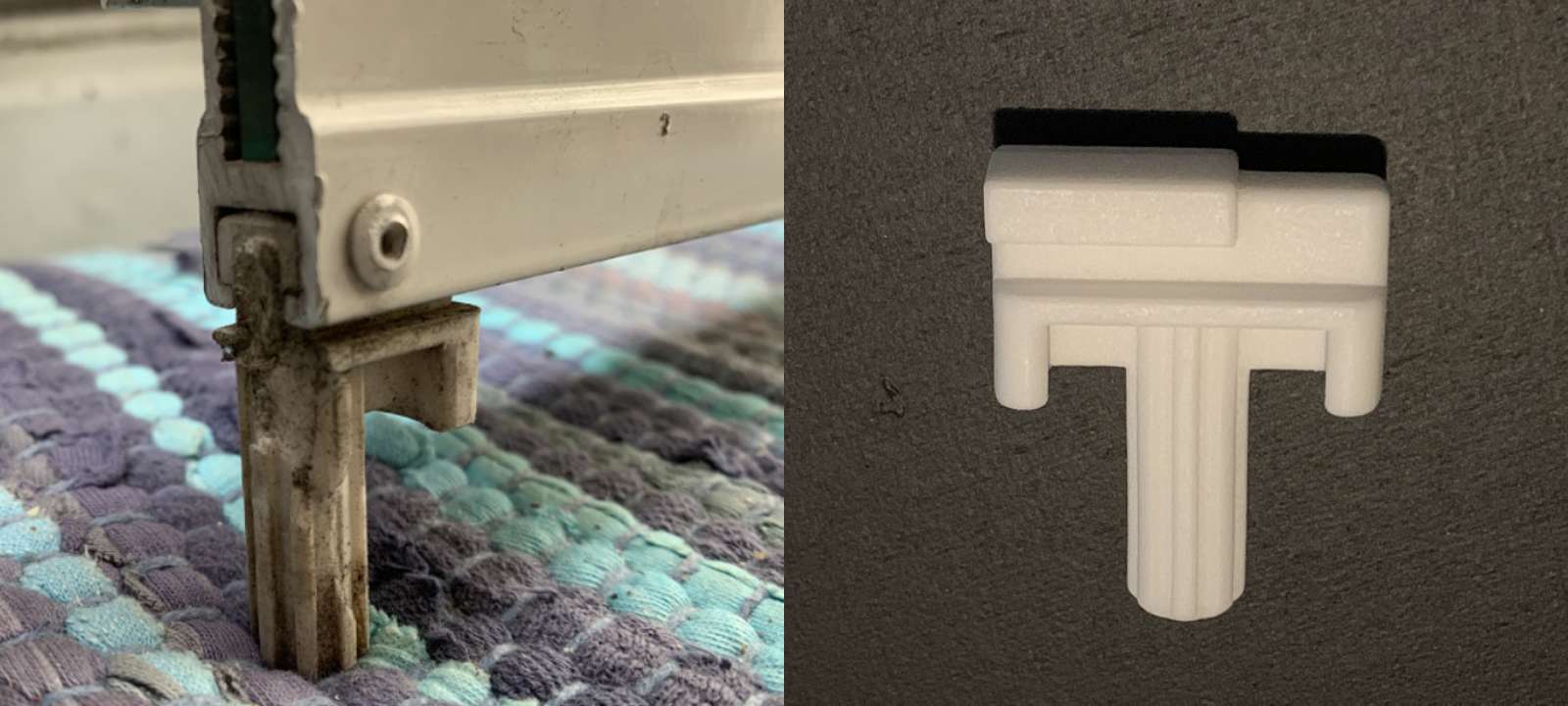
“Renewing all the plastics in balcony glazing system the housing company can get away with roughly one third of the cost compared to changing a new system. Problem so far has been that the plastic parts have not been available. There has been many companies on the market and most of them dont exist anymore” Tells Jöran Wargh from PL Varaosat. Jöran knows what he is talking about as he has been in the industry for over 10 years. This specific problem is what started his company PL-Varaosat. PL-Varaosat sells installs and does maintenance to these systems. “A while ago I was doing maintenance to an old system and we had to make spare parts manually from sheet metal to get the system up and working. I thought to myself that this makes no sense. There has to be a better way. The push came to shove when an old customer aquired if we have some spare-parts for them.”
The solution
3D-printing has turned out to be the key component in starting up PL-Varaosat business. Mr. Wargh is skilled in 3D-modeling and he started to build a library of digital parts based on the old, sometimes broken parts. Its no easy task. Materflow served as a manufacturing parter to make the physical products. At this moment there is more than 250 parts in the library. The whole market probably requires more than 500 models to cover the needs of the customers. On top of supplying parts to older generation systems PL-Varaosat also offers the latest most popular models as a retail partner. The product portoflio of the company is very extensive by all metrics.
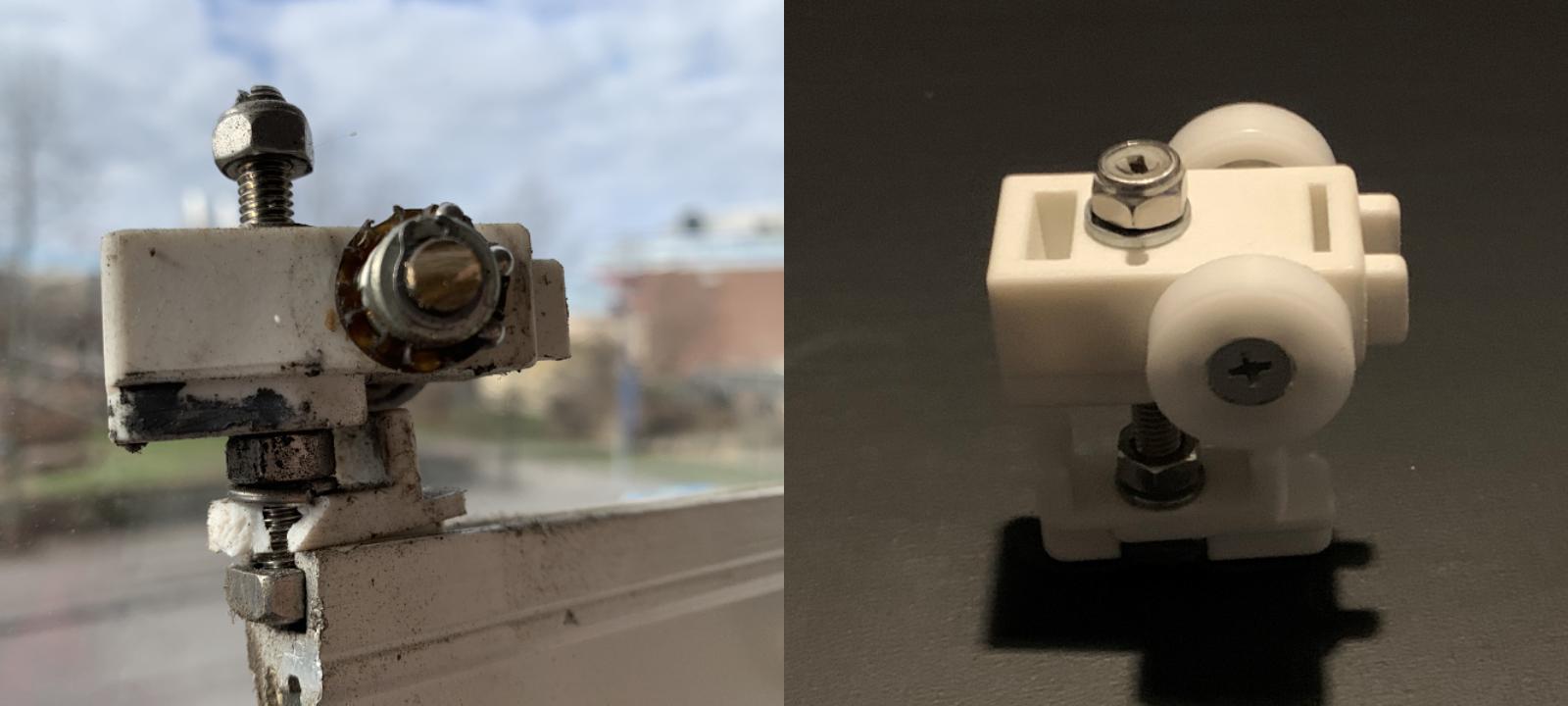
3D-printing is vital for PL-Varaosat for many reasons. Making molds for such a large quantity of products would not be very feasible. There is also the added benefit of getting to market faster and simply utilizing a digital supply chain makes every step in the process easier and more cost efficient. Products are built by demand so no large stock is required. Response time with on-demand manufacturing is fast enough to fullfill requirements of the end-use customer. “The most common items we do keep in stock but other than that all parts are built by customer requirements. Modeling of old products we do free of charge, we only invoice the quantity ordered.” Says Mr. Wargh on operating the young e-commerce business.
Paving the way for digital spare parts
This type digital sparepart is starting to catch up all over the world and in Finland too. Proven concept is becoming a common practise. Many large companies like Daimler, have mapped their extensive part catalogies those items that are suitable for additive manufacturing. In addition to manufacturing cost a lot of saving can be accomplished simply due reduced warhousing need. Logistics can also be simplified as on-demand manufacturing allows less complex process chain. Digital spare parts have been extensively studied by Aalto university and VTT. Published article By VTT
In addition to manufacturing Materflow helps companies to optimize for additive so the full benefit can be utilized. Faster printing at lower cost is the typical result.