Five false notions: The truth about 3D printing
Based on a digital model the 3D printing process builds a three dimensional object layer by layer. A levelled way to describe a technology that’s inherently multi-dimensional. 3D printing has been around since the 1980’s but in the public eye the concept is still clouded with inaccuracies and misconceptions. Before we bust any 3D printing myths let’s have a quick recap on history and terminology:
- In 1974 a British chemist and author David E. H. Jones comes up with the concept of 3D printing and publishes his thoughts in the New Scientist magazine.
- In the 1980’s several researchers around the world develop the concept and the basics of the technology are formed. Many of these inventions have kept their significance to date.
- In 1986 a US inventor/entrepreneur Charles W. Hull founds a company called 3D Systems Corporation and is the first to commercialise the technology.
- Various 3D printing techniques and titles have been developed over the years (Stereolithography, Fused Deposition Modeling, Selective Laser Sintering, Selective Laser Melting, Direct Metal Laser Sintering…). The techniques can differ in many ways (e.g. raw materials, production process, machine technology) but the basic idea is the same: Based on a digital model the 3D printing process builds a three dimensional object layer by layer.
- In casual, popular language 3D printing and Additive Manufacturing (AM) are basically synonyms for additive technologies, referring to the theme of material being added.
- In an industrial context 3D printing might refer to a subset of AM technologies.
The common perception of 3D printing is led on by the media. Clickbait news usually include the cute cubic shaped desktop printers churning out fidget spinners or the gloom and doom of home made firearms.
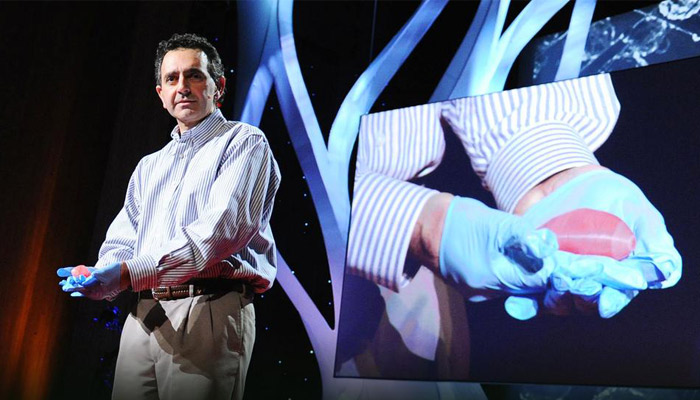
The industrial side of things hands a grander perspective. Car bodies and parts, houses, and even human parts are already 3D printable. Industries from aviation to electronics and medical to food have adopted 3D printing for product development (rapid prototyping) but also in growing numbers for producing spare parts and fully functional end products replacing conventional production methods in the process. It seems that one of the few limitations that 3D printing has is the lack of imagination in product development.
Still some die hard false notions of industrial 3D printing exist. We decided to name a few based on our experience:
1. Anything can be 3D printed.
Not true. Not yet anyway. There are almost no constraints when it comes to complex shapes and geometries but material and size does matter. At Materflow we employ machines capable of printing fairly large objects e.g. prototypes and scale models (max 280x280x365mm for metals, max 320x320x600mm for plastics). We’re also specialised in printing cost-effective series of spare parts and end use products from various metal and plastic materials. You can read more about our production and materials here.
2. 3D printing is a sensible manufacturing method only when the shape and geometry of the part is complex.
It’s true that 3D printing outdoes conventional manufacturing methods all day when it comes to complex shapes and geometries. But it doesn’t mean that complexity is a must to reach more reasonable costs and faster delivery times. This stainless steel knob (a flow channel spare part) is a prefect example:
3. Printing is easy and fast. All you have to do is: download the 3D file, press a button, and voilà!
Basically yes, in practice no. Some careful preparation is needed before you can do the printing part. We check and optimise all the 3D files for printing aiming to add and nest as many different parts as possible into a single production run to reach optimal capacity. The more parts in a single run, the cheaper the price per part. Also the printing machines require a certain procedure for every run and some general maintenance every now and then. When the production run is done the printed parts go through basic post processing and other extra services if needed.
4. The quality is always the same regardless of technique or printing machine.
Without a proper knowledge and understanding of the additive manufacturing cycle with all of its aspects you can forget about quality. As stated in the beginning of this article there are various printing techniques and machines each with their own profile and nuances. Professional AM specialists know their craft from optimising the 3D models to selecting the right technique, material, and parameters for printing. You could say that a skilled AM specialist is a mix of product developer / designer / technical engineer / materials engineer. At Materflow we use SLS and SLM techniques for metal and plastic printing. SLS and SLM are widely considered as the best techniques for industrial scale 3D printing.
Post processing procedures are almost equally important to quality as the printing itself. All the printed parts get the same treatment: We collect and recycle the material leftovers, clean all flow channels and holes, enhance the surface quality with glass bead blasting and if necessary will also do other stuff like polishing, dyeing, paint works or coating. For the most part post processing is manual work but over the years we’ve developed and refined the processes to include some automation which has cut the processing time significantly.
5. If I place my order today are the parts ready for delivery tomorrow?
In case of emergency, possibly. As said, we aim to go for full capacity production runs to optimise cost per part. A normal run takes a day or two, the post processing depending on your need, plus standard delivery times with different carriers. Consult our AM specialists for more info.
Materflow designs and produces 3D printed metal and plastic parts for industrial use. Our customers operate in the industrial sector with ambitions in developing their products, supply chains, and processes towards more profitable and sustainable solutions. In addition to 3D printing services we help our customers develop and implement 3D printing into their design and engineering processes.